3-Step Value Stream Management (VSMgt) Simulation
This 3 step simulation exercise will explore the service side of the car factory, so instead of assembling new cars, we repair them. This event requires the use of any of the LeanMan Car Factory Kits or Packages, as shown in the compatible products section. If you have not yet purchased one of Car Factory Kits, now is a good time to add one to your cart.
The pre-event activity sets up the room arrangement using at least four tables, with participant placemats at each, and tent-cards with titles at each position. Customer cars are assembled ahead of the event, but with added problems. Mismatched wheel color; extra or missing brakes; extra or missing head or tail lights; non-rotating wheels, etc.
THE EVENT
- The person acting as the customer will return cars at random for evaluation and repair. Sometimes the customer wants to approve the repair after evaluation and before repair, and works this through the administrator.
- The customer administrator must receive the order, determine warranty or at cost, and create the work order. Sometimes the customer wants to approve the work after evaluation and before repair is initiated, so communication to the evaluation team is established.
- The service technician receives the order and evaluates the work then either performs repairs that can be made immediately or requisitions the needed parts. If waiting parts, stores the item until parts arrive, then sends the car to a repair technician to perform the repair and complete the order. Recording metrics such as the time and materials used.
- The quality technician inspects the repairs, and rejects errors back to the technician.
- The stockroom obtains the materials and delivers the parts to the repair person. To add reality, a unique amount of time is added for the delivery person to wait before delivering the part, thus simulating independence and other priorities of the support department.
As the simulation runs, all steps must complete correctly and the appropriate information recorded on paperwork to create orders, requisition parts, perform repairs, inspection acceptance, review repair labor and material used and to create an invoice. etc.
The challenge will be to create a lean information flow, very visual, accessible by all who need to know it, and prioritized appropriately. This sequencing is a point to observe between non-lean and lean flow. Each of these times require some bit of available capacity, which must be scheduled into the next available time slot and the customer administrator advised of the estimated completion time so the customer can be advised. On-time metrics will measure actual to estimated completion and overall turn around times.
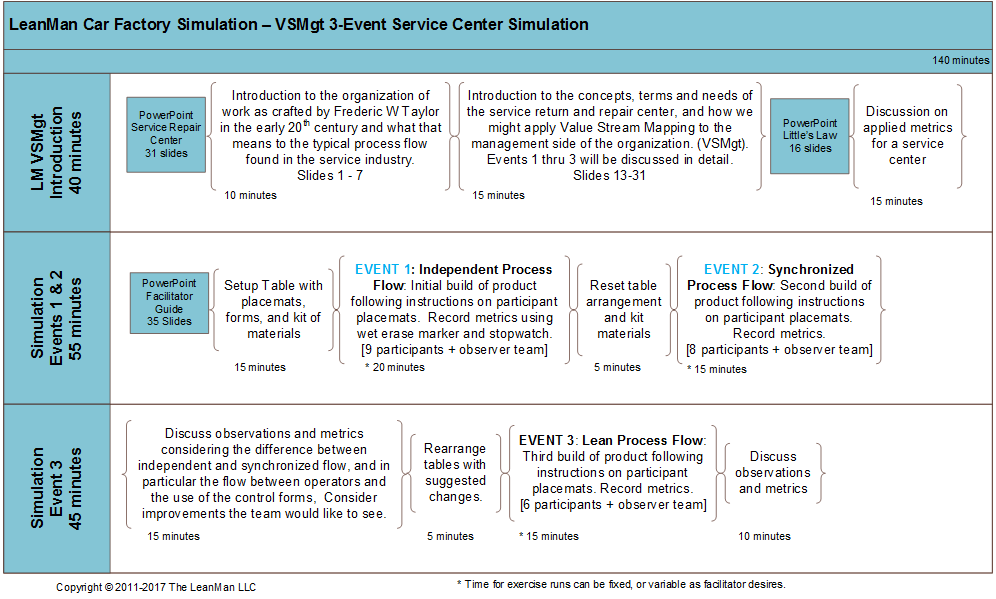
NUMBER OF PARTICIPANTS
The First event requires about 9 participants, with two of them performing transportation duties. A few more participants can easily be added if necessary by creating a detail rework stage with head and tail lamp repair. (Note: The head and tail light material is available at any office supply store. See the Read Me file on the USB Drive for information.) Additional participants acting as observers are also welcome and provide the facilitator with support during the between-rounds discussions.
This simulation event works well with shop technicians and service center workers, but is also a good training experience for administration staff and customer support managers because it delves into the role expectation of a customer support team.
EVENT TIME
Event time is about 2 to 2 1/2 hours for the simulations and discussions between runs, plus PowerPoint presentation used. Room size should be medium to large conference room, allowing at least four tables per team and seating 2 people per table. Be sure to allow room for observers and for the conveyance people to move materials between the departments. Allow additional time before the event to pre-assemble the customer cars.
Deluxe Car Factory Simulation
$563.68
LeanMan Grand Car Factory Simulation
$2,044.90
The LeanMan Grand Simulation Package is a reduced cost bundle of the Deluxe Car Factory Simulation, the VSM, the Kanban and the Heijunka events packaged into two double-deep containers. Now on SALE! Save $200.00