The LeanMan Deluxe-PLUS Kanban Simulation is a complete Lean Principles training package. In addition to all of the materials and presentations of the Deluxe Kit, the package includes materials to create a full customer-pull value stream flow and to explore all of the tools and communication techniques of Kanban along the way. See Deluxe Car Factory Kit
Customer-Pull Kanban Simulation
The addition of the Kanban kit supplies the extra materials needed to turn your Deluxe kit into a fully integrated customer-driven value stream "from customer to factory to supplier."
This simulation training will help participants understand how lean philosophy and techniques can be applied in a totally random mixed-mode customer-pull product flow utilizing Kanban cards and other Kanban signaling devices to control flow and inventory levels. It even provides an opportunity to use Heijunka planning to level production.
The event is the Zoom-Zoom Car Factory and Showroom. Customers take delivery from the Show Room at random, which triggers stock replacement from the factory Warehouse, which then triggers the Planning Dept to order a replenishment from the Factory, which in turn causes a duplicate car to flow back into the Show Room. Along the way, various Kanban methods are employed.
The LM Kanban Simulation is presented in four events - all four are a full value stream and utilize Kaizen and inventory metrics to analyze flow; the last two events utilize the Heijunka planning method and Heijunka box to sequence flow. All events calculate the Earned Value; Margin as a percent of sales; and Inventory levels. All four events also introduce Little's Law metrics equation TH = WIP x CT. See Fun with Little's Law.
- NUMBER OF PARTICIPANTS - The event set up is variable but works best when the Factory and the Show Room are separated by some space such that a Conveyance person is required. The Warehouse can also be separated from the Factory if there is adequate space available. The minimum number of participants is 7, then Conveyance people, Observers, and Metrics people can be added as needed.
- FACILITATION - A single facilitator can easily control the team when using the printed and laminated participant place mat instruction sheets. The laminated sheets include Heijunka calculator charts and wet erase markers, plus the Excel 10-Second Test, the Earned Value and Margin Calculator, and the Inventory metric calculators aid in keeping track of bottom line improvements.
- EVENT TIME - Event time is approximately 1 hour per event step, but depends upon the facilitator and how much time is spent on focusing on specific opportunities such as inventory control, or Kanban techniques, or financial metrics for each flow type.
The Kanban Simulation events #3 and #4 include instructions for using the LeanMan Heijunka Box, and while not absolutely necessary, the LeanMan Heijunka Upgrade Kit is highly recommended to obtain the Heijunka Box and gain the full impact of the training experience. However, the Readme file facilitator notes will provide an adequate albeit less fun alternate method to perform the event without the Heijunka Box.
The Deluxe Kit contains over 300 parts, packaged in a durable container with a Polycarbonate cover that latches securely to hold the materials for travel. Approximate dimensions of the double-deep Plus kit container are 16 9/16” x 13 1/8” x 4 1/8”.
The Deluxe Kit contains several Microsoft Power Point training presentation files. The first is a 4-step simulation training setup guide, which the trainer can customize to fit the specific training situation being taught, plus some forms for tallying metrics.
The Lean Factory Simulation training begins with the Batch ‘n Queue method based on Adam Smith’s division of labor principles. These were later solidified by Frederic W. Taylor and presented in his 1911 book “The Principles of Scientific Management” (New York: Harper & Brothers). Taylor’s methods became the bedrock for production flows around the world, where companies learned to divide functions into small departments, each organizing their activities into batch processes to optimize their own independent needs and goals.
The second presentation is a history of the manufacturing methods leading up to Lean Mfg., and provides detail concepts behind each of the training simulations. Both presentations may be customized to include your company logo and edited to focus on your specific needs.
The batch process is nicely presented in the New Manufacturing Challenge: Techniques for Continuous Improvement by Kiyoshi Suzaki (The Free Press, 1987), and it is Suzaki’s model that becomes the first simulation event step.
The next event step transitions to the techniques of one-piece cellular flow with MRP push; then continuous flow with Kanban signals; and finally ending with a lean flow using a demand pull system.
Along the way, additional lean concepts are layered onto each event, such as Value Stream Mapping, learning to see waste with the NVA test, and more. There are four main flow concepts presented and fully described in the kit, plus many suggestions for training the participants to think lean.
The simulated product is a small car that is easily assembled and disassembled, in a take along package that provides the trainer with an excellent reusable lean concept training tool. The LeanMan Deluxe Lean Factory Simulation Kit provides enough materials to train an average class of 5 to 9 individuals, with opportunity for each individual to have hands-on participation time in at least one event.
The Deluxe Car Kit includes materials to simulate the influence of non value-adding activities like fixturing and containers that are returned upstream, and the impact of material defects to flow. Certain components of the toy car have been selected to emphasize naturally occurring human influences that contribute to a learning curve, while other influences are inserted by design. The importance of having both components of variability, natural and imposed, is essential to presenting a true simulation or real shop conditions. The result is a design that closely mimics real factory conditions with very realistic metrics from team to team.
Note: see Why not Legos? See how to get started with Lean: Getting Started with Lean.
Each of the 20 assembled cars is easily disassembled and all materials are completely reusable. There are also observation roles participants might fill to gather information on each flow method as it unfolds. The Deluxe Kit includes the 10-Second Test waste manager along with the facilitator notes for the TPS 6 exercise event that leads from a 5-pc Batch 'n Queue to 1x1 Lean Flow with 2-Bin Kanban material. Each exercise ends with Financial Metrics and an analysis of the 8 wastes. These exercises and observations provide the class with discussion material that can be used to explore:
- Value Adding and Non-Value Adding activities associated with each flow type,
- Effects of each flow on quality,
- Ideas that form the basis for continuous improvement Kaizen event ideas
- Certified Assembler concepts
- Work Balance and Takt Time concepts
- Point of Use (POU) shop inventories methods
- Value stream mapping techniques
Kanban
An important and overridding control element in production scheduling based on "pushing" the demand is that the quality of the demand forecast that must achieve a successful "push” is rarely accurate unless the customer orders are highly repetitive. Fortunate indeed are those with such steady customers.
Kanban, by contrast, approaches control by receiving the "pull" from the demand of the customer. Therefore, the supply or production is determined according to the actual demand of the customers. In contexts where supply time is lengthy and demand is difficult to forecast, the best you can hope to do is to create a rapid response capability to meet the demand.
This is exactly what a kanban system can help to achieve: It is used as a demand signal that immediately propagates through the supply chain. This can be used to ensure that intermediate buffer stocks held in the supply chain are better managed, and usually smaller.
Along the way, various kanban methods are employed.
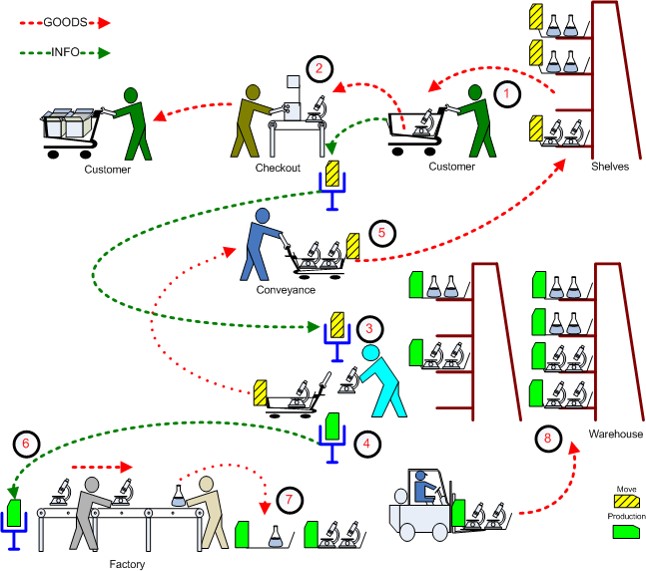
Kanban can be visual, such as the raising of a signal flag to request another delivery of a predetermined quantity of something; or sending a golf ball down a tube to alert the person at the other end it is time to act.
Kanban cards can be a single card system that control flow throughout the process or more commonly, a dual card system where Move kanban cards control the flow between the customer and the finished goods warehouse, and a Production kanban controls the factory process. For example, a kanban card specifying an exact model or type of an item is used to deliver the product from the warehouse to the customer, which in turn can cause additional kanbans to trigger release of replenishment parts further upstream at the factory, until eventually the supplier is alerted to deliver more raw materials.
If customer demand is unpredictable the use of the heijunka planning menthod and sequencing box can further help to control buffer inventory levels while maximizing the throughput rate and excellent on-time delivery metrics.
Q: What is the difference in training provided between the Deluxe
Plus VSM Simulation Value Stream event and the Deluxe
Plus Kanban Simulation which is also a full Value Stream?
A: There are two distinct versions of the VSM training:
The Deluxe Plus VSM Package is a 9-step transformation process going from a non-lean batch ‘n queue type push flow to eventually become a lean pull flow. There are positions for Customer, Supplier, Warehouse, Factory Assembly, Quality, and Finished Goods/Shipping. Each point process is improved during the transformation, but the bottom line is flow doesn’t really occur until the whole value stream is working together. During each event you have observers looking for waste. After each event you hold a kaizen event to discuss observations, count inventory at each point process, discuss buffer inventories and visual communication techniques. This event is an all-day experience and focuses on the tools of lean such as target cards, kaizen discussions, etc. The two Car Factory Kits supplied in the package provide sufficient materials to allow a continuous loop run of each transformation step for as long as the facilitator wants or needs to get the points across. There is a lot of WIP in the stream during the initial rounds. In the last event a mixed-mode operation with the red, blue and plain color cars is included. Earned value is calculated as a metric. In general, consider this package as a beginner to intermediate level VSM training product.The Deluxe Plus Kanban Simulation Package includes an enhancement to the Deluxe Kit Car Factory which adds the same materials supplied in The LeanMan Kanban Upgrade kit. It is also a full value stream with a customer, a showroom, a factory with a planner function, a warehouse and finished goods area. This event starts out fairly lean and does not deal so much with the transformation from the old ways of the 1990’s but instead focuses on tweaking a value stream for production leveling in a random customer pull environment. The production is a full mixed-mode operation with six variations of the car produced and “sold” in the showroom. Takt time, flow metrics and Little’s Law are introduced. The tools used are kanban methods such as signal flags, buffer stocks, kanban squares, kanban MOVE and kanban PRODUCTION cards, and heijunka leveling techniques.The extra materials provided in the kanban kit are red and blue cars, extra MOVE and PRODUCTION kanban cards, kanban posts, signal flags and the laminated participant placemats and facilitator guide. The event is a half day exercise designed to explore 4 different ways of operating a lean value stream, and the available performance improvements with each added method. In general, consider this product an intermediate to advanced VSM training product.
Plus, it's probably the most fun lean training event available anywhere!
The files are provided on CD and USB Flash Drive, and include additional free bonus presentation materials. These short presentations provide supporting concepts and training necessary to fully implement the lean principles into your organization.
The presentations may be used as is, or edited for your specific training need and audience.
Included files are:
- The Five Principles of Lean - 8 slides
This presentation can be used as a baseline for introducing the student to the five principles of lean as outlined in the book: Lean Thinking by James Womack et al. Edit the PowerPoint slides to add focus for your specific training event.
- 14 Philosophies behind TPS - 15 slides
Excerpts from The Toyota Way by Jeffrey Liker, this presentation provides the 14 guiding philosophies developed by the Toyoda family and other contributors that are the foundation for the Toyota Production System.Note: The concepts and terms presented in The Toyota Way book are the basis for two fun and challenging games available from The LeanMan. See the tab Team Development: TPS ToyodaWay Game Set on CD.
- 5-S for Lean - 35 slides
This presentation can be used as a baseline for a 5-S program. It contains the basics for understanding 5-S and a great starter program to set your workplace in order and prepare it for Lean. Edit the PowerPoint file to suit your needs.Note: The concepts and terms of 5-S are the basis for two fun and challenging games available from The LeanMan. See the tab Team Development: 5-S Game Set.
- Visual Control for Lean - 13 slides
This presentation can be used as a baseline for a Visual Control program to provide visual communications in the shop area. Coupled with the 5-S presentation, it sets the stage for powerful and fast team communication so everyone knows what, when, where and how the product flows. Edit the PowerPoint slides to suit your needs.
- Visual Systems for Lean - 46 slides
This presentation can be used as an introduction to Visual Systems and 5-S. It focuses on the concepts of seeing new meaning behind everyday sights, and works well to support The LeanMan Learning to See the Waste and The LeanMan Developing Lean Eyes presentations. Edit the PowerPoint slide to add photos from your own workplace.
The LeanMan 26 question Lean Self-Assessment Tool is also provided to help you assess your team's present Lean maturity level and readiness to implement the principles of lean into your organization.
The LeanMan suggests using the Deluxe PLUS KANBAN Car Factory Simulation in the following simulations:
Learning to See the Waste
This executive level 2-Step simulation is the simplest event to run but packs a big WOW factor. It requires just one Car Factory Kit per team. Plus, with the laminated participant instruction placemats, it's so easy to perform that single person can easily facilitate five or more teams, making it great for large audiences and conventions.
- Group Size: 5-8
- Duration: 100 min.
- Steps: 2
Car Factory Simulation
This 4-step simulation uses one Car Factory Kit per team, and a single facilitator can easily run 2 or 3 teams in parallel for a little competition and metrics comparison. This simulation event is also provided as an editable set of files on the USB drive that allow customization to the facilitator's specific target training needs.
- Group Size: 5-8
- Duration: 100 min.
- Steps: 4
Large Group Simulation
Purchased as a separate supporting product (it is included in the Grand Package), this simulation is used with multiple Car Factory Kits to expand the event size to accommodate larger groups for an introductory Lean experience. The 4-step simulation is designed as an introduction to Lean for variable sized groups of participants in the four main flow methods.
- Group Size: 5-39
- Duration: 60-150 min.
- Steps: 2 or 4
TPS Simulation
The Toyota Production System (TPS) simulation is a 5-step event which uses the training methods generally recognized as the Toyota method for introducing lean flow. This method focus more on flow and eliminating process waste and less on reducing the number of human elements in the process.
- Group Size: 8-12
- Duration: 110 min.
- Steps: 5
VSMgt Service & Repair Center
Purchased as a separate supporting product (it is included in the Grand Package), this 3 step simulation exercise will explore the service side of the car factory, so instead of assembling new cars, we repair them. Value Stream Management concepts are used to improve flow door-to-door in this unique and fun exercise. This simulation requires purchase of at least one of the LeanMan Car Factory Kits or Deluxe Packages.
- Group Size: 9-12
- Duration: 140 min.
- Steps: 3
Kanban Simulation
This four-step Customer-Pull event explores the flow control differences between a single kanban card and dual kanban card replenishment system with random demand in a full value stream simulation.
- Group Size: 8-12
- Duration: 260 min.
- Steps: 4